What is Porosity in Welding: Important Tips for Getting Flawless Welds
What is Porosity in Welding: Important Tips for Getting Flawless Welds
Blog Article
Comprehending Porosity in Welding: Checking Out Causes, Impacts, and Avoidance Strategies
As professionals in the welding market are well mindful, recognizing the reasons, results, and prevention methods related to porosity is critical for accomplishing robust and reputable welds. By delving right into the origin triggers of porosity, examining its damaging effects on weld high quality, and checking out reliable avoidance approaches, welders can enhance their expertise and abilities to generate premium welds continually.
Common Causes of Porosity
Contamination, in the kind of dirt, oil, or rust on the welding surface area, produces gas pockets when warmed, leading to porosity in the weld. Inappropriate securing occurs when the shielding gas, commonly made use of in procedures like MIG and TIG welding, is not able to completely secure the molten weld pool from reacting with the surrounding air, resulting in gas entrapment and succeeding porosity. Furthermore, poor gas insurance coverage, often due to inaccurate circulation rates or nozzle positioning, can leave components of the weld unguarded, permitting porosity to form.
Impacts on Weld High Quality
The existence of porosity in a weld can substantially compromise the total quality and stability of the welded joint. Porosity within a weld produces gaps or tooth cavities that compromise the structure, making it extra prone to fracturing, deterioration, and mechanical failure. These gaps act as tension concentrators, reducing the load-bearing ability of the weld and increasing the possibility of premature failing under applied anxiety. Furthermore, porosity can additionally function as possible sites for hydrogen entrapment, additional aggravating the destruction of the weld's mechanical residential properties.
Moreover, porosity can prevent the efficiency of non-destructive screening (NDT) methods, making it testing to spot various other flaws or interruptions within the weld. This can lead to significant safety and security issues, specifically in critical applications where the architectural integrity of the welded parts is extremely important.
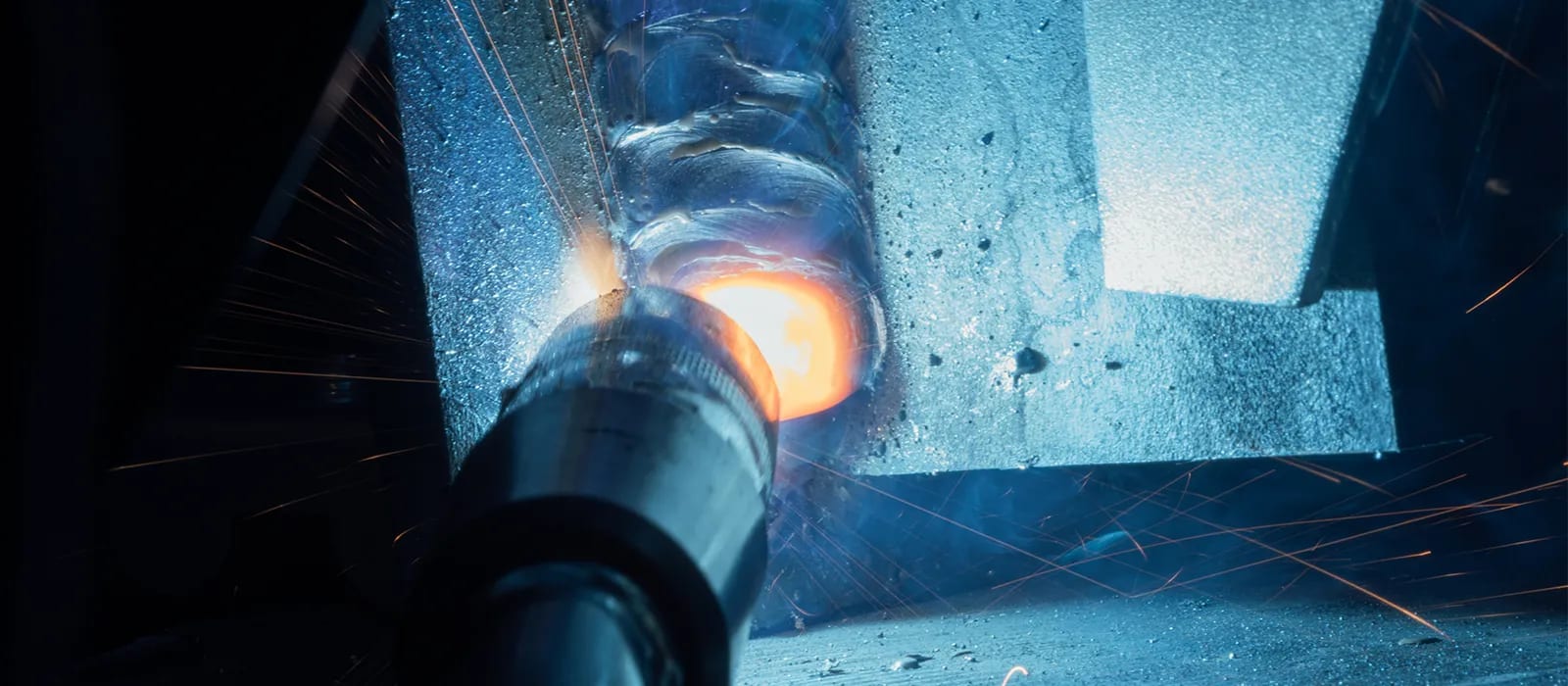
Prevention Techniques Review
Offered the damaging impact of porosity on weld quality, effective prevention strategies are important to preserving the structural integrity of bonded joints. Furthermore, selecting the suitable welding criteria, such as voltage, existing, and take a trip rate, can help reduce the risk of porosity formation. By integrating these prevention techniques right into welding practices, the occurrence of porosity visite site can be significantly lowered, leading to more powerful and much more reliable bonded joints.
Importance of Appropriate Protecting
Appropriate shielding in welding plays a vital role in preventing atmospheric contamination and making certain the stability of welded joints. Protecting gases, such as argon, helium, or a combination of both, are typically made use of to safeguard the weld swimming pool from responding with components airborne like oxygen and nitrogen. When these reactive components come into call with the warm weld swimming pool, they can create porosity, causing weak welds with reduced mechanical residential properties.

Insufficient shielding can lead to different issues like porosity, spatter, and oxidation, jeopardizing the architectural stability of the welded joint. Adhering to correct securing practices is essential to create top notch welds with very little defects and make sure the durability and reliability of the bonded parts.
Surveillance and Control Methods
Just how can welders efficiently check and manage the welding procedure to make sure optimum outcomes and stop problems like porosity? By continuously monitoring these variables, welders can determine deviations from the perfect problems and make prompt adjustments to stop porosity formation.

Additionally, applying correct training programs for welders is important for keeping an eye on and managing the welding process successfully. What is Porosity. Informing welders on the relevance of preserving consistent criteria, such as proper gas protecting and take a trip rate, can assist stop porosity problems. Normal evaluations and certifications can additionally make certain that welders are efficient in tracking and regulating welding procedures
In addition, the usage of automated welding systems can enhance tracking and control capabilities. These systems can specifically regulate welding parameters, lowering the likelihood of human error and guaranteeing consistent weld top quality. By incorporating innovative surveillance technologies, training programs, and automated systems, welders can properly check and regulate the welding process to lessen porosity issues and accomplish high-grade welds.
Final Thought

Report this page